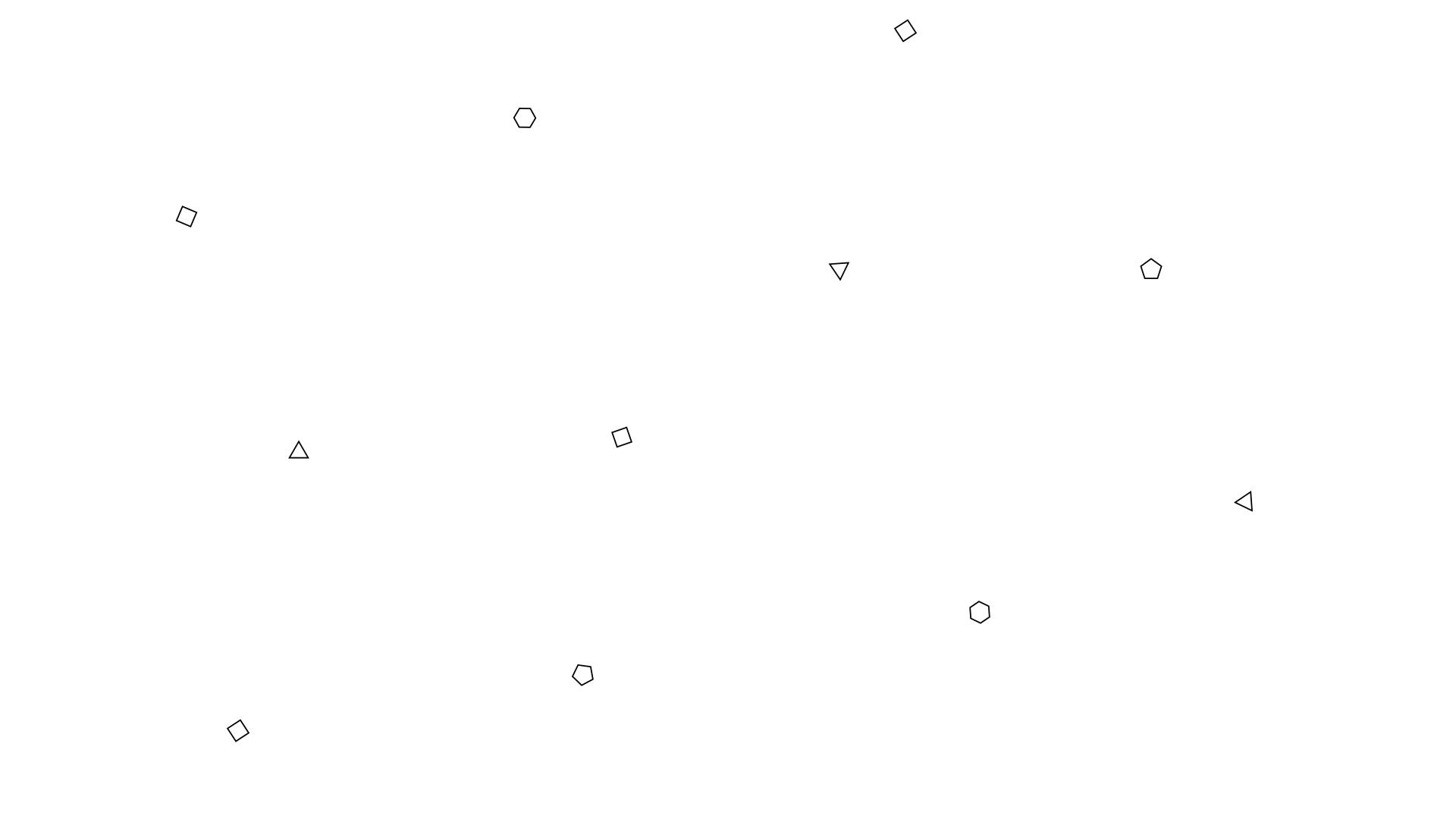
Electrical Guides
How to Wire a Basic Control System
This guide is for new electrical members to wire a basic control system. *Reference pictures are on their way!*
​
Parts:
-
Battery
​​
-
120 amp CB
The 120 amp circuit breaker (CB) is used to enable power to go from the battery to the
Power Distribution Panel (PDP) and other parts of the robot. To turn on the CB, push in the small ON switch (the small lever). The OFF button is located on the top of the CB. Push it all the way down to safely cut power from the battery to the rest of the robot.
​
-
PDP
The PDP distributes power to the Robo RIO, the VRM, the CAN circuit and other necessary motor controllers. To open each power port insert a WAGO and push along the top. After reaching the end of the Wago port, push in and lever the Wago screwdriver up until the port below open and you can fit your wire into the bottom port.
-
20, 30, and 40 Amp Fuses
The fuses allow electricity to flow from the PDP to other parts of the robot through the ports mentioned in the paragraph above. The larger the numbers are, the more electricity is allowed to flow through the PDP. Make sure to look up the minimum amps needed to safely use parts. We can always use smaller amp breakers than needed, but if we use one that is too large, we could risk sending too much electricity to our components and damaging the hardware.
40: Talon SRX, Victor SP+SPX, Sparkmax
30: Compressor (normally plugged into PCM)
20: Spikes, Lights.
-
VRM
The Voltage Regulator Module (VRM) Limits the amount of power that is distributed to the wireless bridge (plugged into 12A/2V).
​
-
Wireless bridge
The wireless bridge enables communication between the robot and our computer by creating a wifi signal for the computers to connect to.
​
-
RoboRIO
Stores all of the programming code and controls the robot. It translates our controller inputs to robot functions.
​
-
RSL
The Robot Signal Light (RSL) signals when a robot is off, on, or enabled. When the robot is off, the light is dark. When the robot is on, but disabled, the light will be solid orange. When the robot is enabled and running, the light will be blinding orange.
​
-
Motor controllers
Motor controllers use our inputs to send different amounts of electricity to the motors, varying the speed outputted.
Talon SRX (CAN signal)-preferred on the drive train due to more data communicated compared to victors.
Falcons (CAN signal)-A motor that has a TalonSRX and Encoder built into it.
Sparkmax (CAN or PWM signal)-Can also be used to control brushless motors
Victor SP (PWM signal)-preferred on minor motors that don't need extreme precision. I.E. Harvester and shooters.
Victor SPX (CAN signal)-Not as powerful as talons, however FRC rules make the less power irrelevant .
​
Process
​
-
Schematics
Schematics are the drawing out of our electronic components and wires. Components and wires are labeled to match the labels we use on our robot. We either draw them out neatly on paper or use google drawings. Our Schematics can be used with the DI/O list for troubleshooting reasons. We try to make it as clear as possible to show the judges at competitions.
-
DI/O list
The digital input/output (DI/O) list is the list where we write every component, where it’s connected, its function, and the label programming assigned it. We must work closely with programming in order to find how our labels connect with their assigned names in their code. These labels are then put onto an I/O sheet for us to refer to in future troubleshooting.
-
Electrical board design
After we know the electrical board dimensions from build and CAD, we then experiment with the placement of our components to make sure we don't waste any of the space given to us. We do this process through either Google Drawings or Tinkercad. We need to make sure to measure our components before creating them on the digital board; we may also use the site we bought our components on to find these dimensions. One thing to note, is we also need to consider space for holes so we can zip tie the wires down.
-
Drilling and layout
Before our board is cut, we first use a sharpie to recreate our board with the dimensions we were given. We then lay out all our electrical components onto the board according to the layout that we made. If the components and wires look like they will fit, then we will proceed to cut the board with a jig saw...make sure to grab a mentor for this!
Once the board is cut, mark where we need to drill with a sharpie, then use a prick-punch piloting tool where the sharpie mark is to create a divot for the drill. *Safety FIRST* Before drilling we make sure a mentor knows we are drilling and wear eye protection. We smooth out holes made by the drills with a deburring tool. We lastly screw in all our components.
-
Wiring
Start by connecting your PDP and 120 amp breaker. Plug in RIO (22 gauge wire) in the bottom right of the PDP labeled "Vbat CONTROLLER PWR" using a Wago to push down the buttons before fitting the wires. Plug the other end of the wire into the RoboRIO into the port labeled "INPUT". Red wire=V(voltage) Black=C(control). After this we connect the PDP and RoboRIO through the "CAN" wiring ports. Yellow indicates high, green indicates low.
​
Plug the VRM through the bottom left port of the PDP labeled "Vbat VRM PCM PWR." (18 awg). The other end of the wire will plug into the port on the VRM Labeled "12Vin".
With the plug made for our wireless bridge, insert the wire end into "12A/2V" on the VRM. Plug the barrel end of the cord into the wireless bridge.
An ethernet cord connects the wireless bridge and the RIO. This will be inserted in the innermost ethernet port on the wireless bridge, and the port on the RIO.
The outermost ethernet port is for when programming needs to reformat the bridge.
We need to include an RSL. To do this, we use a two pin connector pre-attached to an 22awg wire. The La and Lb ports need to be jumped. To do this, a small additional red wire is needed. A diagram on how to do this is shown in the diagram below.
​
​
Motor controllers
For Talon SRX and Victor SPX, plug the red "V+" and black "GND" wires into their respective connectors coming off of the PDP. The points labeled "M+" and "M-" will be wired directly to the motor with their respective colors (white=red green=black). These motor controllers have CAN (yellow and green wires) which are wired through one another rather than all plugging into a central spot. This is called chaining. This can be done directly off components or through connectors through CAN buses or other connectors.
For Victor SP or Sparkmax, plug the red, "V+" and black, "GND" wires into their respective connectors coming off of the PDP. The points labeled "M+" and "M-" wire to the motor with their respective colors (white=red green=black).This controller uses PWM (black red and white, red is not used) This is plugged directly into the RoboRIO labeled PWM
​
Congratulations! If you followed these steps, you should have a programmable, drivable robot!
